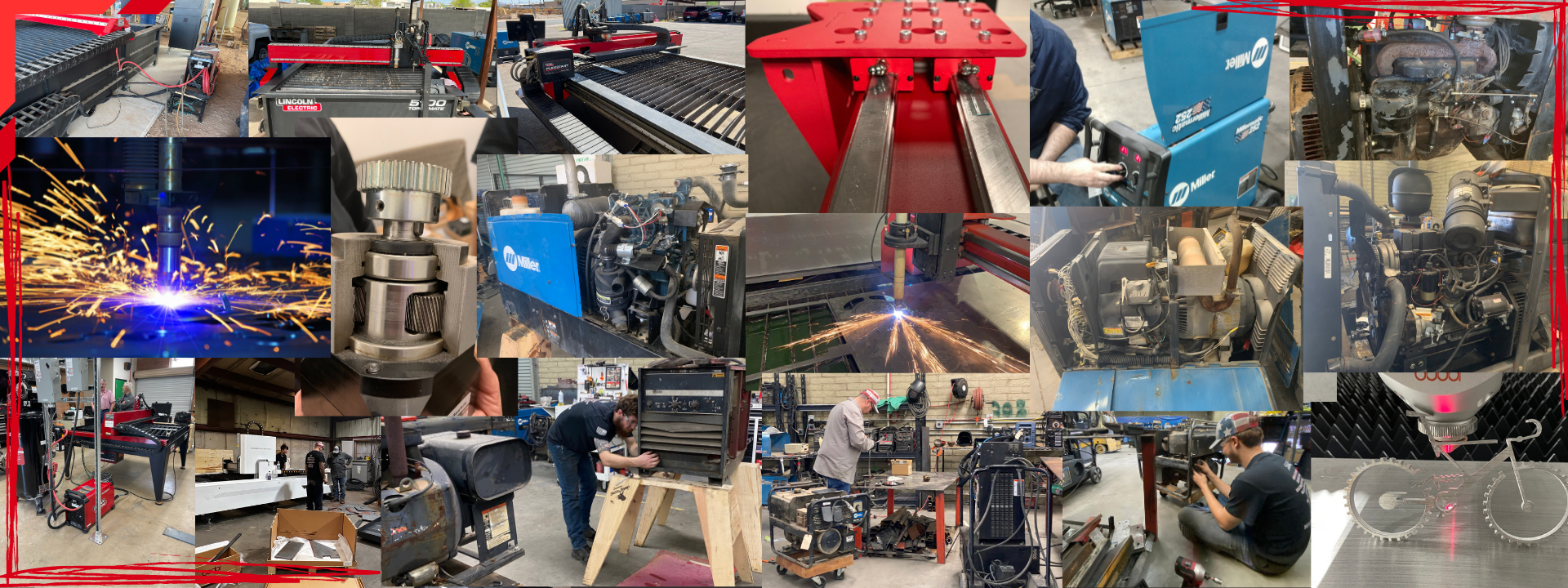
Planned Maintenance
Planned maintenance agreements specifically tailored to meet individual customer needs.
Stacking Up the Benefits of Planned Maintenance
"If it ain't broke, don't fix it" worked back in a day when machinery was simpler and cheaper to both buy and fix... However, modern technology and equipment are far more complex. Today's more appropriate philosophy:
If it ain't broke, let’s work to keep it that way.
Top 20 reasons for planned maintenance:
1. Minimizes / eliminates costly downtimes - increases profitable uptime.
2. Minimizes / eliminates machinery failures - potentially catastrophic.
3. Reduces unscheduled maintenance - repairs can be made when they least affect production.
4. Reduces spare parts inventories - many parts can be purchased just before scheduled shut-downs.
5. Optimizes machinery performance so it always operates within specifications.
6. Reduces excessive electric power consumption caused by inefficient machinery performance - saves money on energy requirements.
7. Reduces the need for standby equipment or additional floor space to cover excessive downtime - less capital investment required for equipment or plant.
8. Increases plant capacity.
9. Reduces depreciation of capital investment caused by poor machinery maintenance - well-maintained machinery lasts longer & performs better.
10. Reduces unnecessary repairs - repairs are done only if performance is less than optimal.
11. Reduces the number of dissatisfied customers or lost customers due to poor quality - with less than optimal machine performance, quality always suffers.
12. Reduces rework of goods caused by less than optimal machine operation.
13. Reduces scrap caused by poorly performing machinery.
14. Reduces overtime needed to make up for lost production due to broken down or poorly performing machinery.
15. Reduces late deliveries caused by broken down or poorly performing machinery.
16. Reduces warranty claims due to poor product quality caused by poorly performing machinery.
17. Increases machinery safety - injuries are often caused by poorly performing machinery.
18. Reduces safety penalties levied against a company for unsafe machinery.
19. Reduces the time required to make machinery repairs - advance notice of machinery condition permits more efficient organization of the repair process.
20. Increases ease of operation of machinery.
Planned Maintenance is especially important for Mechanized Plasma Systems.
Murphy's Law says the plasma-cutting machine will always break down when you need it most-- usually right in the middle of that biggest plate-cutting job. At up to $200 per hour or more fully burdened, downtime on the cutting machine gets expensive.
Many shops do not have a regularly planned maintenance schedule for their plasma cutting systems. After a few months of neglect, the cutting machine will no longer perform as designed. Fine mechanical parts will prematurely wear causing rough machine motion. This may lead to out-of-tolerance parts and poor cut quality - particularly at higher cutting speeds. The Plasma system is vulnerable to contamination and may malfunction and misfire causing cut quality and torch height control problems not to mention reducing consumable life and can cause damage that will lead to expensive repairs and downtime.
When components in the machine fail, troubleshooting the problem and servicing the machine can take days. Sticking to a regular schedule of planned maintenance can avert most of these problems.